Soft drinks manufacturer increases production and achieves energy savings
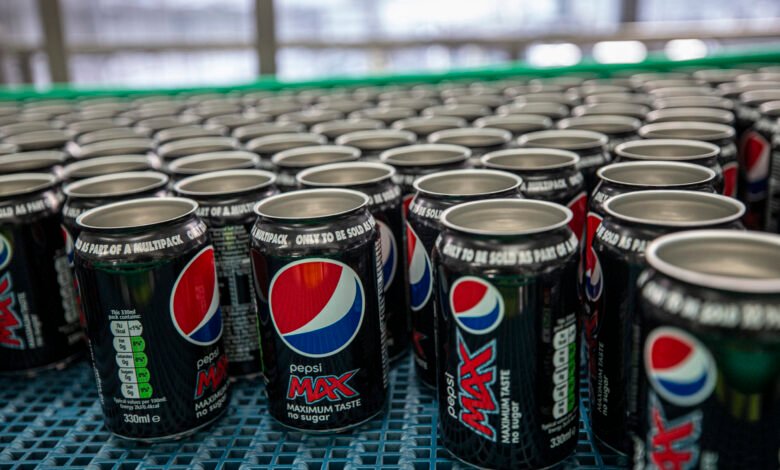
The time-sensitive, overnight installation and commissioning of an advanced custom turnkey solution with four booster sets has increased production for Britvic, supporting the company’s growth plans. The system upgrade, supplied by Grundfos, also achieved a reduction in wastewater and energy usage, with the reduced carbon footprint supporting the company’s sustainability agenda.
Britvic is an international soft drinks business rich in history and heritage. Founded in England in the 1930s, it has grown into a global organisation with 37 much-loved brands sold in over 100 countries. The company combines its leading brand portfolio, including Fruit Shoot, Robinsons, Tango, J2O, London Essence, Teisseire and MiWadi, with PepsiCo brands such as Pepsi, 7UP and Lipton Ice Tea which Britvic produces and sells in Great Britain and Ireland, under exclusive PepsiCo agreements.
With an increase in demand for soft drinks and high energy consumption for moving the water required for their soft drink production, Britvic turned to Grundfos to look at options to increase production and reduce energy consumption across their plant in Rugby, United Kingdom.
Britvic was looking to support its sustainability agenda, focusing on its ‘Healthier People, Healthier Planet’ strategy, where the company is committed to creating a better tomorrow and delivering timely responses to the health and environmental challenges currently faced on a global level. Britvic has fully integrated the UN Sustainable Development Goals into this strategy and aligned objectives and targets with these goals. It was important to Britvic to select a supplier that supports this ambition and lives and breathes these goals. Grundfos, with its own ambition of contributing to the UN’s Sustainable Development Goals (SDG) #6, Clean Water and Sanitation, and SDG #13, Climate Action, was the perfect match.
“Improving our cooling system means that the chilled beverage water supplied to production stays cooler, resulting in faster production and higher output,” said Calvin Winch, Engineer, Operations Development GB&I, at Britvic.
“Specifically, we were looking at acquiring a pumping solution that helps us meet our sustainability goals by reducing wastewater and energy usage, resulting in a reduced carbon footprint and improved water efficiency.”
The situation
Water is essential to Britvic’s production processes and widely used throughout its value chain. An element of this includes the heating and cooling of water at its factory in Rugby – a process that provides the opportunity to explore alternative ways to manage Britvic’s water use and protect this vital resource.
“Because we have an excellent working relationship with Britvic, simply spending time on site working with their staff meant we were able to identify possible production improvements. This made it possible for us to advise Britvic and work with them towards an optimised, tailored solution,” said Mark Bennett, National Business Development Manager, End User Industry, at Grundfos. “For a system upgrade, I highly recommended our advanced digital offering Grundfos iSOLUTIONS, which utilises intelligent pumps, cloud connectivity and digital services. Together they enable real-time monitoring, remote control, fault prediction and system optimisation to help meet the level of performance needed in a demanding manufacturing site.”
Grundfos performed an ‘Energy Check Advanced’ to measure the actual energy use in the system. This is not simply a ‘nameplate’ check of efficiency; sensors are placed in the system to get the live data from the existing setup, helping operators find potential energy savings in their pumps.
The proven and validated measurements help Britvic support its ‘Healthier People, Healthier Planet’ strategy and the focus on energy and carbon emissions reduction using science-based Scope 1-3 targets to attain a sustainable supply chain.
The solution
To help achieve these twin goals, the recommended Grundfos solution was a full turnkey project consisting of four Grundfos Hydro MPC-E booster sets. The booster sets were custom built for Duty/Assist/Standby operation, delivering the optimal amount of chilled water to the facility’s production lines, to allow for the high-speed filling of cans. Each installed booster set incorporated three Grundfos CR pumps with integrated speed control.
Grundfos booster sets are designed to use multiple pumps to maintain a constant delivery flow or pressure at maximum energy efficiency. When demand increases or decreases, you will still experience a constant water supply. This is achieved using the Grundfos CU352 controller, which ensures the pump set operates at its best performance.
This intelligent booster set adapts automatically to a site’s varying demand 24/7. The new generation of inline vertical multistage centrifugal (CR) pumps can be used in a wide range of applications and are designed for world-class efficiency and reliability – with millions of customisable solutions.
Eight weeks were set aside for design and build, including a limited 18-hour overnight installation and commissioning window. The booster sets installed were connected to the Britvic PLC via the Grundfos Communication cards.
The Grundfos manufacturing site in Sunderland, UK, means that Grundfos can offer quick response time, offering customers the greatest flexibility when it comes to achieving bespoke, custom, offsite build solutions. These come as plug-and-play, helping to achieve minimal disruption when installed at the manufacturing site.
The outcome
With the new booster sets and improved cooling system, Britvic has achieved the increase in production it wished for, helping meet increased demand and future-proofing the production line. As the beverage water stays cooler and temperature control has improved, faster production with an increased output is now possible, as more cans can be filled.
This project also helps Britvic work towards its sustainability goals with total energy savings of £374,420 per year expected with the four new booster sets (as of September 2022). The existing system consumed over 60kW per set, and this is now reduced to less than 20kW per system, with the future-proof flow included. The return on investment (ROI) is less than twelve months. With complete control over the system, Britvic now also experiences a reduction in wastewater because the optimal amount of water for cooling is being used.
“We have set ambitious sustainability goals for energy reduction, a lowered carbon footprint and water reduction in our beverage production,” added Calvin.
“Grundfos installed an energy, water and cost saving solution with no production disruption through time-sensitive overnight installation and commissioning. This solution future-proofs our business, meeting the increased production demand, and shows when you work closely with your supply partners; we are much more effective, efficient and stronger together”.
“We are very happy to have helped Britvic with validated savings from a solution that contributes to their sustainability agenda, and in a way that is very much in line with our own approach,” concluded Mark.
“And this is only possible because of a strong customer relationship, where our ongoing collaboration shows that we understand Britvic’s challenges. I’m sure the savings we have shown here will lead to further projects together.”