Seal upgrade brings environmental and operational benefits
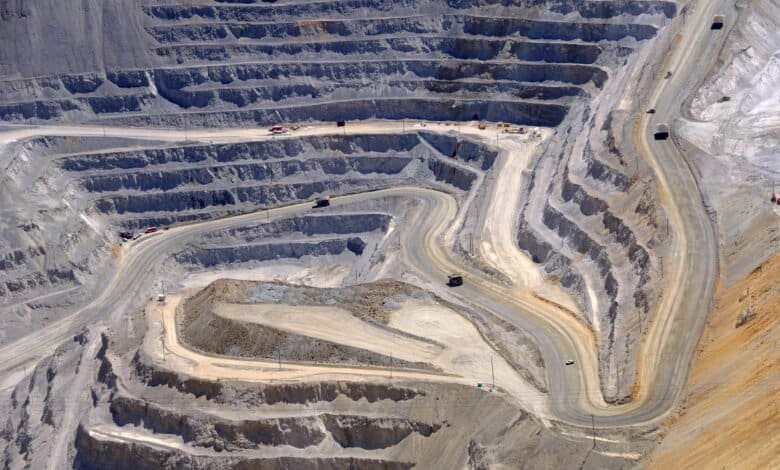
Flow magazine discovered how seal specialist John Crane Helped a Chilean mine cut water use by 95% while improving equipment reliability and reducing maintenance requirements.
One of the world’s leading copper producers operates a large open pit mine located in northern Chile. The mine produces 324,000 tons of copper concentrate each year and approximately 9,800 tons of molybdenum. Rainfall in this region of Chile is increasingly scarce – compounding the already demanding operating conditions, especially in the mine’s critical concentrator grinding and transportation processes. After an internal review, mine management grew concerned about the site’s significant water consumption, caused partly by ageing pump packing systems, amounting to approximately 280 litres of water per minute per pump.
Wanting to significantly lower water usage and waste, as well as improve pump maintenance, reliability and emissions to the atmosphere, mine management worked with John Crane to identify a solution.
The two-year project initially focused on seven grinding and transportation process pumps from three different brands, each with a history of high water consumption. The pumps’ packing system required frequent adjustments and needed to be changed out every second month, which included bearing repairs due to the packing systems’ excessive leakage.
The challenges for John Crane included ensuring the reliability of the pumps and other equipment while reducing water consumption and maintenance. After reviewing the situation and goals, John Crane experts suggested the mine consider a technically superior sealing system upgrade. The upgrade included redesigned mechanical seals with easily changed elements, providing adaptive pump parts – all with safety and efficiency as priorities.
The solution
A 10-inch mechanical seal was designed that does not require disassembly when technicians maintain the wet parts of the pump and is fixed directly to the bearing box for low vibration. The double concentric mechanical seal design incorporates both seal support Plan 54 and Plan 32, allowing the mechanical seal faces to be constantly lubricated and free of solids. The new seal functions on the same operating principles as a conventional mechanical seal but is modified to adapt to the axial spaces of the pumps. Adaptive parts were also introduced during the project, including a stuffing box, sleeves and union elements.
Soon after the project began, the new seal, the Type 5902TS, was put to the test. Even though surrounding water pipes froze during a cold snap, the new seal continued to operate thanks to a mixture of water and glycol included in the Plan 54 seal support system.
The three pumps currently in service have reliably operated for two years without interruption – a significant improvement over the two-month repair/maintenance precedent set prior to the update. Water usage has been reduced by approximately 95%, from 280 litres per minute to about 20 litres per minute, on each pump upgraded with a John Crane mechanical seal, and process fluid/slurry no longer leaks to the atmosphere.
The upgrade eliminates the time-consuming operational adjustments previously required, will not damage the shaft or other pump components, and has increased bearing life.