Capture carbon with side-channel pumps
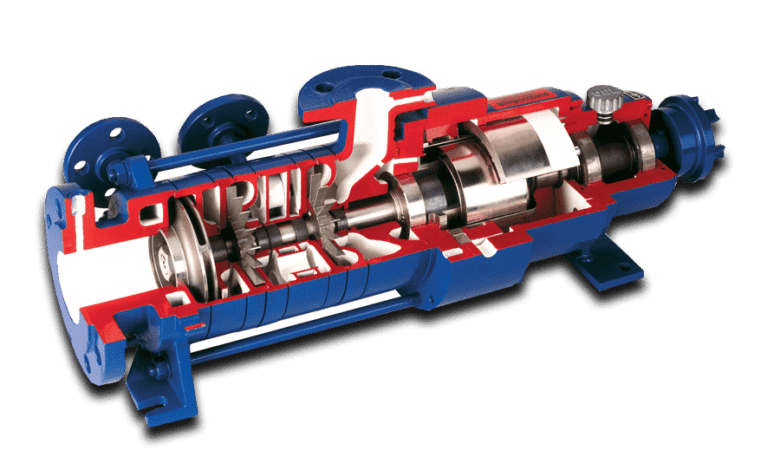
With the ever-present focus on reducing carbon emissions, CDR Pumps, a specialist in chemical process pumps, looks at the role side-channel pumps play in carbon capture and storage plants.
CO2 capture and storage, commonly known as carbon capture and storage (CCS), is a technology used to reduce the release of greenhouse gases and reduce the carbon footprints of a variety of industries. The process involves capturing CO2 from the emissions generated by industrial processes and power plants and storing it in geological formations.
In 2024, builders depend on side-channel pumps to meet the specific requirements of constructing CCS plants. These requirements include low NPSH values, high delivery heads, the ability to withstand extremely low temperatures (down to -60°C), and the capability to handle two-phase flows with up to 50% gas content without damage. Side-channel pumps have been chosen due to their reliability in meeting such demanding criteria.
Capturing and storing CO2 is crucial in the decarbonisation of industrial processes. Currently, CCS plants are mainly being constructed in sectors where significant amounts of greenhouse gas are produced, such as power plants that utilise fossil fuels, the chemical industry, oil and gas refineries, the cement industry, iron and steel mills, and the maritime industries. By capturing and storing CO2 in their applications, it is also possible to generate environmentally friendly energy, such as the production of blue hydrogen or the supply of liquefied CO2 for heating purposes, process engineering, or the shipping industry thereby reducing carbon emissions and promoting sustainability.
Why side-channel pumps?
When using side-channel Pumps in your carbon-capturing process, CO2 is captured, and then it goes through a compression stage where it is subjected to high pressure so that it can be transported as a liquid to its destination for use or storage. The biggest benefit of side-channel pumps is that they meet the technical requirements required, but they can also be used in varying stages of the process, from carbon-capturing through to transportation and on to its final destination, whether that be recycled for use in other applications or solid form and returned to depleted oil fields.
Side-channel pumps have been manufactured to withstand challenging process conditions. These pumps are specifically designed to handle high pressures, reaching up to 100 bar. These pumps are also capable of operating within a wide temperature range, spanning from -60 to +220°C. This versatility allows for the reliable transportation of low-temperature fluids like CO2 and ammonia, which transition from a gaseous to a liquid state at temperatures around -57°C and -33°C, respectively.
The design of side-channel pumps incorporates various features to accommodate these demanding conditions. These include spring assemblies to compensate for thermal expansion and contraction of the hydraulics and elongated inserts which prevent temperature-induced stresses in the pump body. In addition, the bearings will have been optimised to ensure a precise fit, and special thrust washers will be used to minimise the effects of wear and tear and improve operational reliability.
Another advantage of side-channel pumps is their ability to perform even when gasses are present in the fluid. When pressurisation changes and the temperature increases, substances like liquid carbon dioxide and ammonia tend to transition into a gaseous state; side-channel pumps have consistently proven to be reliable over extended periods of time – even with two-phase flows with up to 50% gas content – mitigating concerns related to vapour formation and the potential impact on delivery.
The first CCS plant projects are now underway using side-channel pumps, which show us that they are a valuable asset in carbon capture and storage and have been instrumental in reducing carbon dioxide emissions and promoting sustainability.