Advanced materials help mechanical seals transform the efficiency and sustainability of pumping equipment
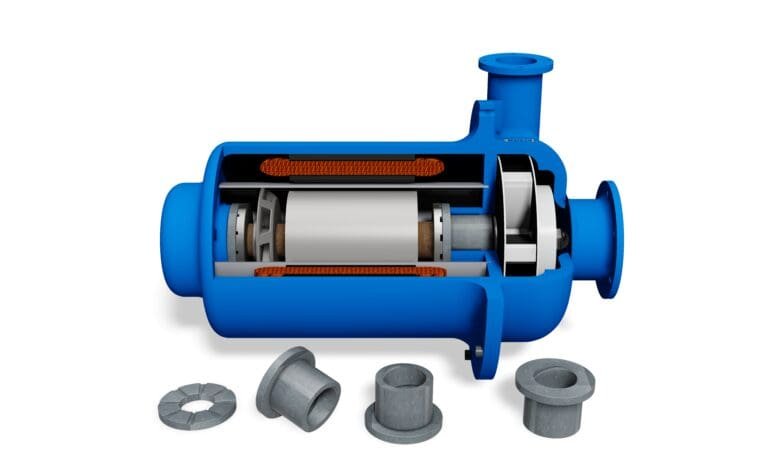
Phillip Charlton, Chairman of the European Sealing Association’s Mechanical Seal Division, explores how carbon-graphite and silicon carbide seal ring wear faces contribute to the energy transition and boost the efficiency of pumps across various industries.
The global energy transition towards sustainable and renewable energy sources requires significant advancements in technology and materials to improve efficiency and reduce waste. In this context, carbon-graphite and silicon carbide (SiC) seal ring wear faces have emerged as critical components in pumping equipment, playing a vital role in enhancing performance, longevity, and energy efficiency.
The importance of pumping equipment in the energy sector
Pumping equipment is essential to various industrial processes, including oil and gas, chemical processing, water treatment, and renewable energy. Efficient pumps are crucial for reducing energy consumption and ensuring the smooth operation of these systems. Mechanical seals, especially those using carbon-graphite and silicon carbide wear faces, are key to maintaining pump reliability, minimising leaks, and reducing energy losses.
How carbon-graphite and silicon carbide materials work
Seal rings are subjected to extreme conditions, such as high temperatures, corrosive environments, and mechanical stress. The choice of materials for these components significantly impacts their durability and efficiency. Carbon graphite and silicon carbide are preferred in modern mechanical seals for the following reasons.
Carbon-graphite wear faces
- Self-lubricating properties: Carbon graphite has excellent self-lubricating characteristics, which reduce friction between the seal faces. This property is essential in preventing wear and extending the life of the mechanical seal, especially in applications where lubrication is limited or unavailable.
- Thermal stability: It can withstand high temperatures without losing its mechanical properties, making it ideal for harsh operating conditions in industries like power generation and chemical processing.
- Chemical resistance: Carbon graphite is highly resistant to chemicals, ensuring it remains effective even in corrosive environments commonly found in the oil and gas and chemical industries.
Silicon carbide (SiC) wear faces
- High hardness and durability: Silicon carbide is one of the hardest materials available, providing exceptional wear resistance and durability. This property significantly extends the lifespan of the seal, reducing the need for frequent replacements and downtime.
- Low friction coefficient: The smooth surface of SiC reduces friction between the seal faces, contributing to lower energy consumption in pumping systems. This efficiency is critical for renewable energy and water treatment applications, where energy savings are a priority.
- Thermal conductivity: Silicon carbide’s high thermal conductivity helps dissipate heat effectively, preventing overheating and maintaining stable operation under extreme conditions.
Enhancing efficiency and sustainability in pumping systems
The use of carbon-graphite and silicon carbide wear faces in mechanical seals directly impacts the energy efficiency and sustainability of pumping systems in several ways.
- Reducing energy consumption: The low friction properties of carbon-graphite and SiC seal faces reduce the energy required to operate pumps. Lower friction means less power is needed to overcome the resistance within the system, leading to significant energy savings over the lifetime of the equipment.
- Extending equipment life: The durability and wear resistance of these materials lead to longer-lasting seals, reducing maintenance needs and the frequency of seal replacements. This extension of equipment life minimises the use of raw materials and energy resources in manufacturing new parts, aligning with the principles of a circular economy.
- Minimising emissions and leakages: Effective mechanical seals made with carbon-graphite and SiC help prevent leaks of fluids and gases. In industries like oil and gas, where preventing fugitive emissions is crucial, these seals play a critical role in reducing environmental impact. They ensure that harmful chemicals or greenhouse gases do not escape into the atmosphere, supporting global efforts to lower carbon footprints.
- Supporting renewable energy applications: In renewable energy sectors, such as wind, solar, and hydropower, pumps equipped with efficient seals are essential for optimal performance. The reliability and energy efficiency provided by carbon-graphite and SiC seals contribute to making renewable energy systems more cost-effective and competitive with traditional energy sources.
Conclusion
The use of carbon-graphite and silicon carbide seal ring wear faces in mechanical seals is transforming the efficiency and sustainability of pumping equipment across various industries. Their unique properties of low friction, high durability, thermal stability, and chemical resistance make them ideal for supporting the energy transition towards more sustainable practices. By enhancing pump efficiency, extending equipment life, and reducing emissions, these advanced materials play a crucial role in optimising industrial processes and contributing to a greener, more energy-efficient future.