Pump compatibility is key
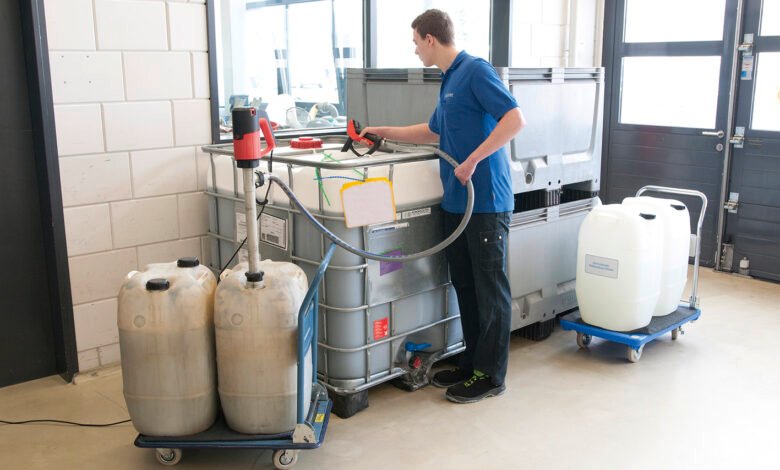
When selecting a pump for a specific application, its suitability for the media being pumped is critical, especially if there are properties which make it a challenging application. Castle Pumps outlines some key considerations you need to make when selecting the best pump for a new application.
When it comes to needing a new pump for your process, “What fluid are you handling?” is one of the first questions you will be asked. Everyone understands that ensuring the wetted parts are in materials compatible with your fluid is vital, as failing to do so can cause the impellers, seals and other components to swell, become brittle, erode or even melt.
Castle Pumps often hears customers saying, “Oh, EPDM is fine for my fluid”, which is a great starting point. But did you know that the concentration and temperature of a chemical can also impact material selection? For example, Hastelloy C is compatible with Hydrochloric acid at 10% concentration at 20°C. However, at 40°C, it has limited resistance.
Not everyone realises that a supplier asking about your fluid is not solely about material selection but also pump selection. So, what else should you be ready to tell your supplier about your fluid when you have a process requiring a pump?
Presence of solids in the liquid
Certain pumping technologies are not suitable for handling even the smallest of particles. Due to the tight tolerances between the casing and the moving parts, vane, gear, and side channel pumps will jam when attempting to pass solids, causing immediate wear. On the other hand, peristaltic and diaphragm pumps can handle solids up to the size of their inlet/outlet. For that reason, sometimes a larger pump than is needed duty-wise is specified to handle the solid size but run at a lower speed.
It’s also important to consider whether the solids are hard and abrasive or soft and malleable. Are they thin and stringy, susceptible to clogging?
Peristaltic pumps have no moving parts that encounter the fluid and, therefore, have no valves, seals or impellers to clog or erode. Whereas other pumping technologies could find stringy solids such as fruit juice pulp wrapping around their impellers. For softer solids, flexible impeller pumps are often a lower-cost solution, thanks to their supple rubber impellers being able to bend around them.
Viscosity of the fluid
Certain designs, such as centrifugal pumps, which are excellent for thin, water-based chemicals, can struggle with thicker fluids due to frictional losses inside the pump, causing flow rates to decline rapidly, whereas many positive displacement pumps excel. Knowing the viscosity of your fluid is therefore very important to pump specification, but also be aware that this can change with temperature. A pump may be able to handle gear oil at 10°C, but at -10°C, it becomes too thick.
In addition, the presence of solids within a thin liquid such as sand in water is much more abrasive than larger solids in a higher viscosity, lubricating fluid such as oil. The continuous cavities between the rotor and stator of the progressive cavity design and the slight flexibility of the stator means that large solids in think liquids can be easily handled. However, when an abrasive water-based liquid is pumped, wear can occur more prematurely than a peristaltic pump with limited internal components.
Is the fluid shear sensitive?
Shear-sensitive fluids are those that, under force, can be damaged or altered, like cream being whipped, shampoo frothing or solids being crushed like fruit pieces in a yoghurt. Awareness of your fluid’s delicate nature can impact the specified pump type. While centrifugal pumps apply high shear in operation, shear-sensitive pump designs such as progressive cavity, flexible impeller, and peristaltic pumps can keep such fluids intact due to their low internal velocity and the wider tolerances between their pump casing and internal components.
Essentially, it is important to give your pump supplier or system designer full details of the fluid you plan to pump, and where available, providing an MSDS sheet is the most accurate way of ensuring compatibility. When it comes to fuel and oils, users should always specify any additives that may get added afterwards. The liquid’s temperature and concentration should also be confirmed if it’s a chemical, as this can impact material selection. While the liquid’s viscosity is important information to share as well. If you aren’t sure about the exact viscosity of your fluid, you can liken it to a more well-known liquid.