Focusing on the driven component
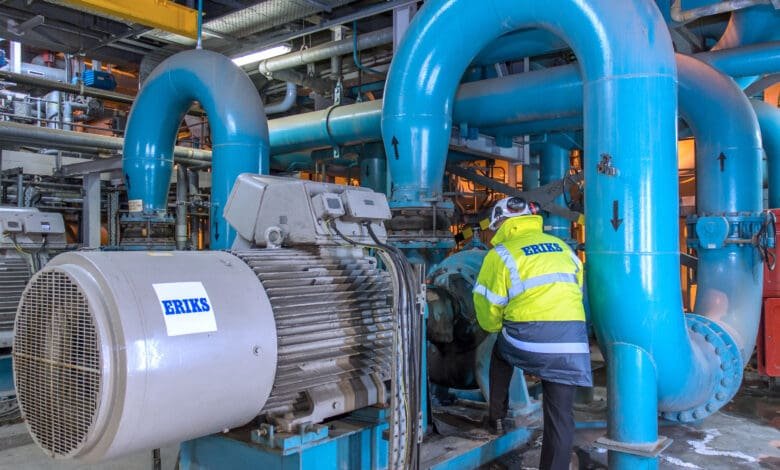
With electric motors creeping upwards in terms of efficiency, the savings to be made by moving between IE classifications are becoming relatively small. However, if we focus on the driven component – such as pumps – as opposed to the driving component, there are still large efficiencies and improvements to be had. BPMA member and pump maintenance and repair specialist, ERIKS, assess how to get the best out of pumps and pumping systems.
With a major focus currently on sustainability and environmental best practice, much of ERIKS’ focus is about returning to first principles when performance testing a pump. To create the data necessary to assess the pump curve, you need to understand the flow rates, pressures it delivers, and the power consumption measured at the motor or from the control panel. Modern technology makes it possible to test the performance of pumps in a non-intrusive way. Ultrasonic flow meters that clip to the outside of a pipe, pressure transducers that measure the suction and discharge pressure and power measuring equipment.
Testing pumps in-situ is important as there’s a recognition that if you test a pump in the factory, it’s efficient to the curve but not necessarily the application. When a pump is tested in situ, if it’s found to be a bad fit, then there are a host of actions that can be taken to rectify the problem, from adding a new controller to trimming or changing the impeller.
The ability to change a pumping system is important because, as we have seen in the water industry, the network has changed and not kept up with the demand placed upon it and therefore the pumps that are in the network are not operating as efficiently as they could be. The potential energy savings in this example are significant – 10 to 15% or, in some extreme cases, as much as 20 or 30%. This thinking is true across a whole range of industries, from steelworks to chemical plants. Essentially, if the infrastructure has changed, either by expanding or decreasing, then the pumps need to be reviewed for optimisation, and while there’s a fine line where VSDs come into their own, in many cases, the solution might be more extreme, perhaps to install multiple pumps with one running permanently and one only operating at peak demand for example.
The battle with obsolescence
Obsolescence is an issue that has to be dealt with on a recurring basis. It can be linked to changes in a process or a network, but also where businesses are running older legacy equipment, and therefore, access to spares is challenging (as OEMs may no longer exist or support the equipment being used). It is possible to create a strategy to combat obsolescence with solutions ranging from the condition monitoring of pumps to ensure their condition is known to the scanning of an impeller for re-manufacture to extend the life of the pump.
Today, organisations like ERIKS have the knowledge to re-engineer and re-scope OEM equipment, either when the condition monitoring indicates or perhaps working to a timed plan of once every five years.
Alongside the ability to re-engineer pumps, coatings are also available that can, in many cases, bring pumps back from the brink to a point where they are serviceable and working within the expected range. The coatings can improve the efficiency of the unit or enable the pumps to handle abrasive material or certain chemicals, for example.
Making big gains
Pumps, by the nature of their application, are open to upgrades, which, in a world where flexibility is key, is important. Efficiency improvements can be made; material improvements can be made, including the use of composite materials that improve efficiency and help reduce MTBR (Mean Time Between Repairs). The geometry of impellers and, in some instances, the casing can be made to be more efficient; the coupling arrangement can also be altered to eliminate historical factors such as misalignment to reduce high vibration. There’s huge scope for making a pump fit a system due to the variability in the system in which it is used, from the cleanliness of the product it is pumping to control technology. When ERIKS looks at things from the customer’s point of view, like the maintenance or energy manager, they would mostly focus on the driven component rather than the driving component. Motors are already efficient, but due to system changes and incorrect pump sizing, there is a lot of headroom for improvement. With the current focus of businesses on energy efficiency and to be more environmentally friendly and sustainable, pump assets represent an opportunity to make great strides.