Energy efficiency – are attitudes changing?
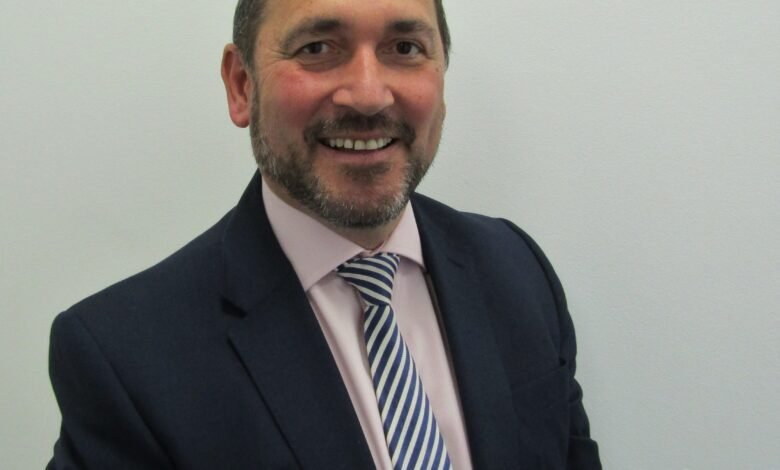
Steve Schofield, CEO of the British Pump Manufacturers’ Association, considers whether there is, at last, a change in attitude towards energy efficiency amongst the general public. And if so, whether this can have a meaningful impact on decreasing energy consumption across UK industry.
The subject of energy, or rather energy efficiency, has long been a topic of vague disinterest among the majority of households and billpayers. Energy, or rather the complex business sector that produces and delivers it, has historically struggled with engagement. Energy efficiency, in particular, has more often than not been misrepresented as simply a penny-saving exercise involving the change of lightbulbs for modern replacements, and switching lights off when rooms are unoccupied. Boiling the kettle less is another suggestion often heard.
However, with the huge global rise in the cost of energy and its near constant headline coverage by the broadcast media, not to mention the financial pain we are all now enduring, perhaps 2023 has the potential to see a real change in attitude. A change that could positively impact all aspects of energy use.
Of course, greater autonomy in our energy provision is now understood and acknowledged as a stand-out way to protect ourselves from market volatility caused by unstable regimes.
But the drive for improved efficiency across all the avenues of energy use will simply mean that the energy we do produce and secure as a country will go that much further. This will not only allow us to make big savings on our domestic bills and ensure our homes stay warm through the winter months, but it will also have a massive impact on the efficiency and, ultimately, the profitability of our commercial and industrial sectors.
The British Pump Manufacturers Association (BPMA) has been a longstanding advocate of the need for improved energy efficiency across the UK’s vast installed base of pumps and pump systems but also the massive opportunity it presents for significant emissions reductions.
The operation of pumps and their associated systems accounts for around 20% of the world’s entire electrical energy consumption, and in some high-use industrial applications, this can be as much as 25-50% of the total electrical energy usage. Across the European continent pumps are the single largest user of electricity within industry, consuming over 300 TWhpa of electricity, which in turn accounts for over 65 Mton of CO2 emissions.
Unfortunately, the vast majority of pump systems operating today were not originally designed with energy conservation as a major consideration. It is now well documented that rotodynamic pumps, which account for 80% of the installed base across Europe, are between 20-30% oversized. This is usually due to an in-built ‘safety factor’ allowing for potential future uprates or any wear in the pump or fouling of the system. But this simply means they are using far too much energy for the required duty. As such, there is huge potential to save massive amounts of energy if these pumps are properly sized, operated and maintained. In fact, if pump systems are initially designed with energy use in mind and the pumps are optimised for efficiency, a saving of up to 50% in electrical energy can be achieved.
In essence, it is important to know as much about the pump system as possible and to create a pressure/flow profile for the system, as the energy required to drive the pump is directly related to the flow and pressure required.
Energy Audits
It is also important to carry out regular energy audits to help determine where energy use reduction measures can be employed and, in turn, how operating costs can be lowered. The government has estimated that most companies can reduce their energy consumption by 10-20%, and energy audits carried out in accordance with ISO 14414 have shown that savings of 30-50% are not unusual. By reviewing utility bills, you can get an indication of the savings to be made and the investment that you should be prepared to put into the auditing process.
Across most industrial sites, some two-thirds of the total energy consumption is used to power electric motors, an integral part of any pump system. The overall cost associated with operating these essential pieces of equipment throughout their entire life span can be broken down as follows; 5% accounts for the initial purchase/installation costs, 10% for ongoing maintenance and a massive 85% for the energy used to run them.
Clearly, any reduction in the energy consumed by electric motors is important, and with modern designs, that reduction can be as much as 30%. It is also evident that many pumps and motors are constantly operated at full power, irrespective of process needs, something which can be managed with the addition of variable speed drives. So, across Europe’s installed base there is the potential for significant energy savings, savings which can in turn drop to the bottom line and increase the profitability of any business.
Given the amount of energy consumed by pumps in their normal operation and the potential for energy efficiency gains within pump systems, the BPMA has developed the Certified Pump System Auditor Scheme (CPSA).
Through the CPSA, pump engineers are being trained to correctly assess the efficiency of pump systems and to provide appropriate recommendations in order to improve the efficiency of those systems. The CPSA accreditation is achieved by successfully completing a four-day residential course, followed by the satisfactory completion of a pump system audit.
Within the full ESOS Guidance document, the ISO/14414-Pump System Energy Assessment standard is referenced as an auditing methodology that can be accepted by “Lead Assessors” approved by the Environment Agency. Accordingly, it is hoped that CPSA accredited persons (who are trained according to the IS0 14414 standard) will be recommended by Lead Assessors to undertake the pumping system elements of company-wide energy audits.
The next CPSA training course is scheduled for 9th-12th May 2023, details are available at www.bpma-cpsa.co.uk.
It is hoped that with the heightened publicity around the cost of energy and society’s growing appreciation of its importance to our very existence, we will begin to see far greater urgency in the adoption of energy reduction measures across our commercial and industrial sectors.
Ultimately it’s a question of choice and whether businesses are prepared to finally address the ‘Capex vs Opex’ argument and begin to enjoy the long-term financial gains available through improved operational efficiency. The offer being; pay for the new equipment now, and recoup the cost through the energy savings made over its operational life.