Creating a reliable maintenance plan
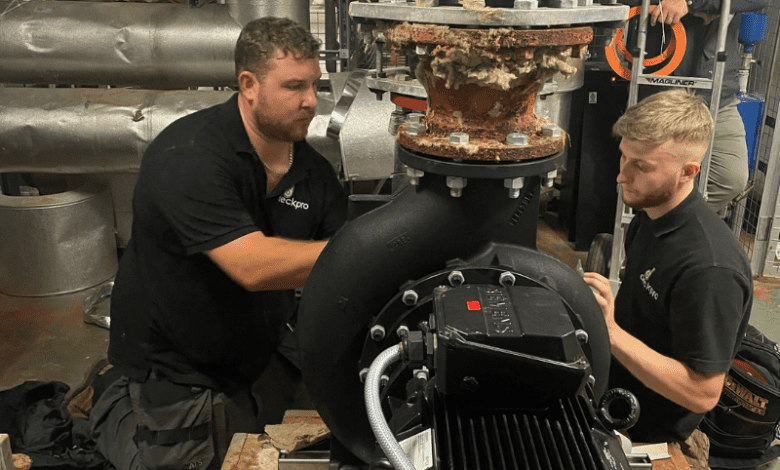
When pumps fail, the consequences can be severe, from flooding and water damage to complete operational shutdowns. One effective way to prevent this – or to foresee potential failures before they happen – is by conducting regular mechanical and electrical checks. Deckpro Pumps looks at what these checks should include, how often they should be performed, and whether there is an ideal time to conduct them.
Mechanical and electrical (M&E) checks enable us to monitor performance, detect deterioration, and flag any issues early to proactively manage risk. The frequency of these checks can vary depending on the specific equipment and its application.
When to carry out checks
In some cases, routine M&E checks align with a site’s maintenance schedule or a company’s processes. For instance, in wastewater applications, the buildup of solids or fats may dictate the frequency of checks – annually, bi-annually, or quarterly.
Industry standards can also guide check frequency. For example, SFG20, the industry standard for building maintenance specification, recommends performing M&E checks on water booster pumps every three months.
Consulting with pump maintenance experts can often provide invaluable insights into the necessary frequency of checks. Working alongside the customer, these specialist companies can tailor maintenance plans according to the specific pump model, equipment requirements, and environmental conditions.
When planning M&E checks, it’s essential to consider the bigger picture and the demands on each pump. Some pumps experience heavy usage during specific periods and may require checks after certain cycles or events. For instance, a production line pump may need inspecting after a set number of cycles, starts, or operating hours.
External factors also play a role. Major weather events, for example, can impact storm and greywater systems, making additional checks valuable after heavy rainfall or flooding, when chambers may accumulate solids.
In larger buildings, heating systems often remain inactive during the summer. When turning winter primary and secondary pumps back on, it’s advisable to carry out M&E checks to ensure safe and efficient operation before reinstating the system.
Essential mechanical and electrical checks
M&E checks vary by pump type, with manufacturers’ guidelines, industry standards, and site requirements often determining a specific maintenance plan. However, there are certain elements that broadly apply to pump inspections.
In most instances, mechanical checks will broadly apply across most pump systems. These include the inspection of pumps for any signs of excessive wear, alignment and coupling checks, checking the condition of the pump mounts, fixings and pipework, and looking for signs of overheating. The pump and motor should be checked for physical damage, paying special attention to rotating parts such as impellers and shafts, bearings, and seals and glands. Any strainer or valve elements should be examined, while gauges, instruments, ventilation slots, and purging points, should also be checked. Finally, performance checks should be made alongside verifying the correct operation of any safety equipment and functions.
In addition to mechanical checks, electrical checks provide insights into a pump’s condition that aren’t always visible, helping to identify issues early and track motor wear over time. These checks should include insulation resistance, running current and voltage checks. The continuity of windings should be assessed, as should the condition of earth bonding and earth loop impedance. Visual checks should be made on the electrical system for any signs of overheating, loose connections, or bad termination. Control checks should be made, including the function of relays, contactors and any remote systems, as should electrical checks of overload equipment such as RCDs. The integration of inverters or local controls should be tested, as should safety equipment and alarm systems.
It’s important to note that all mechanical and electrical checks should be carried out by a trained and competent person.
Joe Smith, Operations Manager at Deckpro Pumps, commented: “In my 12 years at Deckpro, I have seen the importance of M&E checks first-hand. We are able to help customers manage the risk of downtime to their systems, and it’s often the case that our recommended maintenance plans have resulted in preventable failure, saving considerable inconvenience and cost. We’ve had clients approach us following failed pumps, and based on our engineers’ reports, we have been able to give more economical solutions such as overhaul or repair.”
Choosing a reliable partner
When it comes to pump maintenance, thorough inspections are essential. For example, submersible pumps must be removed from their chambers to be inspected properly. Or, a booster pump that’s making unusual noise should be isolated and stripped down to determine the cause and ensure it’s safe to continue operating.
Joe emphasised the importance of avoiding complacency: “I’ve found that preventable failures often stem from subpar routine servicing. I’ve attended sites before where submersible pumps have been ‘serviced’ for years by a pump company. Yet, when I’ve lifted the pumps out of the pit to carry out the necessary mechanical checks, the client is surprised because the other engineers never did that.”
A reliable pump partner will ensure all engineers and technicians are fully trained and certified, with any necessary specialist lifting or safety equipment maintained to industry standards and LOLER regulations. Proper calibration and category selection for electrical test equipment are also essential to ensure accurate, compliant results.
When choosing a pump partner, some criteria are non-negotiable. A trustworthy partner will prioritise minimising client risk, recognising that inadequate maintenance can lead to significant disruption and expense. This partner will plan inspections carefully, conduct checks thoroughly, and offer guidance based on their findings.
A key quality to look for is a partner who provides a detailed maintenance report following each visit. This report should outline all checks completed, identify passes, failures, and advisories, and suggest any necessary remedial actions. A good partner collaborates with clients to establish effective maintenance plans and respond proactively to any issues that arise.
Ultimately, the report should meet your standards and provide actionable insights to help you maintain efficient, reliable pump systems.