A second life for obsolete pumps
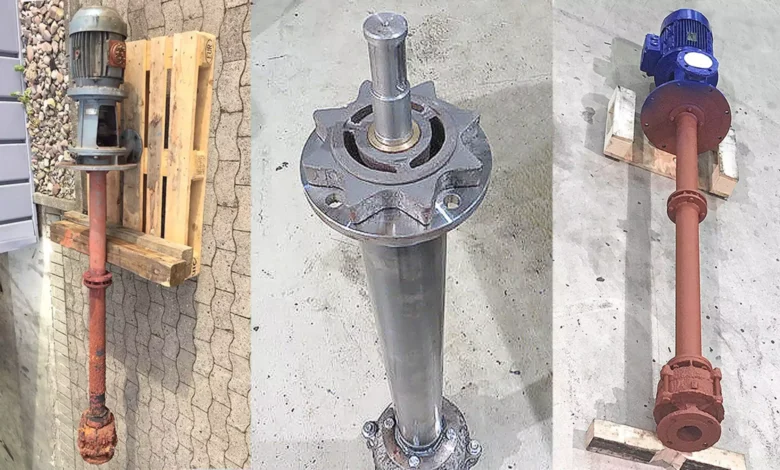
When “aged” machinery in a system fails, spare parts are often no longer available. Buying a new machine is costly and would lead to cost-intensive renovations of further components as well as some downtime of the entire system. KSB has developed a procedure in which spare parts are reproduced by 3D printing. This is particularly helpful in the case of old pumps from different manufacturers. It provides plant operators with fast availability and significant savings.
It is very common these days for power stations to operate vertical centrifugal pumps, which have long exceeded their service life, to transport turbine condensate. Regional energy partner EAM Natur Energie GmbH has been using such a centrifugal pump – made in 1967 – in the HKW Göttingen (combined heat and power station) south of Hannover. Even just by looking at this pump set it was apparent that it had long exceeded its useful life when it finally stopped working. After more than 50 years, it was hardly surprising that procuring spare parts was unsuccessful. In this case, KSB SupremeServ took on the task and was able to repair this third-party product.
No parts available
Oxidised iron had been depositing on the pump for decades. This resulted in magnetite swelling up the surface of the entire pump to such an extent that efficient operation was no longer possible.
The original manufacturer, Halberg, no longer had any spare parts for this pump in its programme, and reproducing the impeller the classic way would have cost nearly as much as buying a new pump.
In addition, if the pump had to be replaced by a new model, costly changes to the entire system, such as piping, valves and condensate tanks, would have been unavoidable.
Individual additive manufacturing
In conformity with DIN ISO 9001 KSB SupremeServ created a detailed damage report and developed an action plan for an economically viable pump repair. Apart from freeing the casing from magnetite using a special mechanical procedure, repairing the centrifugal pump mainly meant replacing its highly complex impellers.
KSB has been involved in the field of additive manufacturing, also commonly known as 3D printing, for over a decade. The largest benefits of additive manufacturing are the high speed at which components can be manufactured and its cost efficiency. Another advantage is the ability to process an immense diversity of materials and shapes, including complex components. Without wanting to outcompete series production by casting, 3D printing is especially suitable for producing single individual components, such as spare parts. It was, therefore, an ideal option for reproducing the two impellers that were no longer available.
At its Pegnitz site, KSB has installed the largest 3D printer worldwide to create workpieces from metal powder using a laser beam. KSB was the first ever manufacturer to receive a TÜV certification for using this method to manufacture components subject to the European Pressure Equipment Directive.
As soon as the CAD data is available, 3D printing is unbeatable in price and enables a procurement time of only a few days. This means KSB can 3D print components that are no longer produced by other pump manufacturers – or that would be very expensive and take months to produce. In this particular case, 3D printing saved three-quarters of the costs.
The process
Using fragments of the old Halberg impellers, a new virtual 3D model was created. In CAD, engineers precisely redesigned the impeller geometry, including the vane curvature, number of vanes, and outlet width. Based on the operating data on the nameplate, the original hydraulic performance data was also reproduced exactly.
In addition to avoiding expensive and time-consuming re-planning of the system, piping, condensate collector and corresponding valves, the new impellers have also enhanced the hydraulic efficiency of all the pumps, resulting in higher energy efficiency, an increased system availability, and therefore clear savings regarding the life cycle costs.
Sustainability in action
Reproducing the new parts has given the pump a second life. With sustainability in mind the KSB SupremeServ has long focussed on repairing old pumps – no matter what their type and make – instead of replacing them with new pumps, which is cost- and labour-intensive.