A cracking upgrade
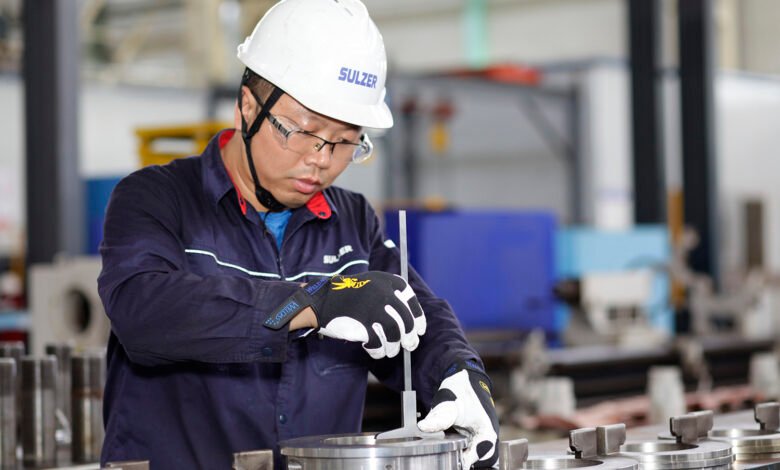
Sulzer’s expertise in rotating equipment retrofits and abrasive services has helped a Philippines-based petrochemical plant solve a persistent reliability issue and prepare for a 64% increase in capacity. Critically for the customer, the solution minimised the need for large-scale on-site modifications while extending pump mean-time-between-failure from less than six weeks to three years.
Located 120km south of the capital, Manila, JG Summit Olefins Corporation’s Batangas Plant is the only naphtha cracker facility in the Philippines. Among other things, it produces ethylene, an essential raw material for the plastics industry. The plant has been in operation since 2014, and rising demand for its products meant that by 2016, the owners were already planning significant capacity upgrades.
However, before those plans could be implemented, the plant’s operators needed to address a critical reliability issue that had emerged during its first years in operation. The Batangas facility uses a proprietary steam cracking technology. In this system, hydrocarbon molecules are broken up at high temperatures in the presence of steam and the resulting product is rapidly cooled to stop the reaction by passing the gas through a heat exchanger and an oil quenching system.
However, this last step was causing concern for the operators. The pumps that moved the quench oil through the system were having issues with the drive end seal barrier pressure dropping and failing frequently, with a mean-time-between-failure (MTBF) of less than six weeks. When a pump failed, the whole process had to be shut down, costing the company more than USD 1m a day in lost output.
Coking damage
Looking to address the problem, the company called in pump specialists from Sulzer to examine the failing equipment, which were ‘between bearing single stage’ (BBS) units that featured a single-stage, radially split, between-bearing design. The initial inspection conducted by the Sulzer team revealed damage to several pump components, including the mechanical seals, impeller, and inlet, consistent with operation in a severely abrasive environment.
Further root-cause analysis of the problem by Sulzer’s abrasive services specialists showed that the culprit was hard carbon coke particles in the oil. Analysis revealed high concentrations of these particles, and many were just large enough (between 75µm and 300µm in diameter) to become trapped between moving and stationary pump components, causing severe wear due to ‘three-body’ abrasion.
Coking is an undesirable but inevitable by-product of the steam cracking process. The build-up of carbon on equipment surfaces leads to a gradual decline in heat transfer efficiency, which in turn accelerates the accumulation of particles. The issue is typically addressed by periodic de-coking of the plant during scheduled shutdowns. The rate of coke accumulation is highly dependent on the characteristics of the hydrocarbon mix being processed; however, in the Batangas plant, this was happening much faster than the designers originally expected.
Selective upgrades
When Sulzer’s engineers checked the build specifications of the failing quench oil pumps, they found that they had been designed with the expectation of a less aggressive operating environment. The main hydraulic components were made using S5 steel, a material susceptible to abrasive wear. Based on their experience of demanding process industry applications around the world, the team proposed a targeted package of upgrades designed to dramatically improve the pumps’ durability in the application.
Those changes included the selective replacement of critical pump components with new parts made from high-chromium C6 steel, together with the addition of an abrasion-resistant SUME SA30 coating on the wetted areas, applied using a high-velocity oxygen fuel (HVOF) process. Sulzer’s specialists also made several detailed changes to the pumps’ geometry, including adding large radii on the edges of the wear rings and extended, contoured sleeves to streamline flow in the pump and minimise the turbulence that accelerates wear. Wear ring clearances within the pumps were increased to allow larger coke particles to pass through them. In addition, at the customer’s request, new ports were also introduced to allow the wear rings to be flushed to remove accumulated particles during pump changeovers.
Flexibility and expertise
One benefit of Sulzer’s retrofit proposal was minimal disruption at the plant. The pumps were upgraded and tested at Sulzer’s facilities, ensuring that they could be reinstalled with no major changes to pipework or ancillary equipment. However, to gain even more value from the project, the plant’s management decided to take the opportunity of the retrofit to make other changes designed to pave the way for future capacity increases.
To meet the customer’s request for a 64% capacity increase and 14% pressure increase in the oil quenching system, Sulzer designed new, larger diameter impellers for the existing pumps. Higher-capacity pumps need more power, so the engineering team specified new motors and couplings for the two electrically powered pumps. They also worked with the original equipment manufacturer (OEM) to implement a package of changes to the turbine, which powered a third pump using process steam. The existing motor base plates were retained and adapted to further minimise costs and streamline project speed, with the old mounting points cut off and new ones welded into place. Finally, one additional motor-driven pump set was added to the system.
Since the completion of the project, the Batangas plant has been able to put its cracker reliability issues behind it. MTBF for the upgraded pumps is now in line with the three-year specified life. Eliminating excessive wear has improved the system’s operating performance, and the oil quench unit is ready to accommodate planned increases in plant output.