Wireless pump monitoring drives efficiency
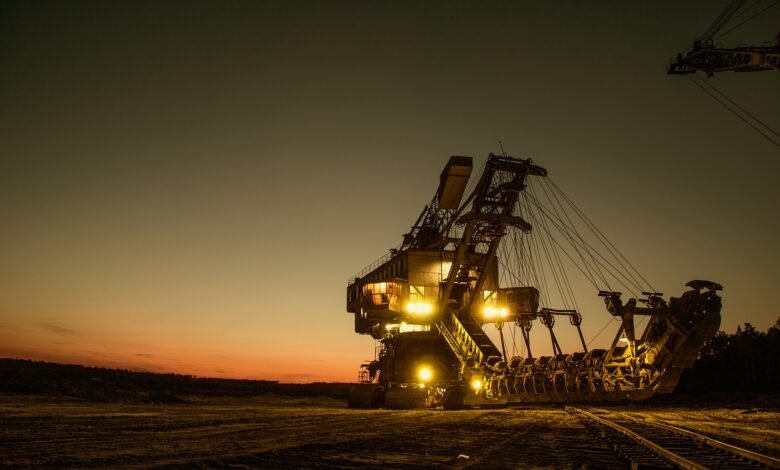
Ian Loudon, International Sales and Marketing Manager at wireless pump monitoring and control specialists Omniflex, discusses how a South African mine uses wireless pump monitoring to keep production efficient.
The Nkomati mine near Machadodorp is one of the largest nickel reserves in South Africa. Having an estimated 408.6 million tonnes of ore grading 0.33% nickel, large amounts of water must be moved around for ore processing and pit dewatering operations.
These processes rely on water pumps and, crucially, pump monitoring systems. Furthermore, because mines are in difficult-to-access, unsafe locations, monitoring pumps isn’t always easy. It’s an expensive task installing control cables through a whole site, so plant managers are increasingly adopting wireless systems – for example, radio telemetry.
Plant managers have used licence band radio frequencies to monitor and control pumps for some time. This system uses controllers and separate radio remote terminal units (RTUs) with a data interfaces. However, maintaining annual radio licences is costly, and much of the equipment becomes obsolete over time. The original equipment manufacturers (OEMs) can no longer support the products because they either went out of business, were sold to other companies, or simply don’t make the products anymore.
With failing and expensive instrumentation, plant managers have no way of monitoring water conditions and switching the pumps on and off. If water can’t be managed or waste can’t be pumped out, the mine’s ability to process concentrate efficiently is put at risk.
The reliable solution
By exploring wireless products that blend radio and controllers into a single DIN rail mounted package, it is possible to control pumps remotely over a large distance. Products like these use licence-free band frequencies to avoid unnecessary engineering and administration. Replacement is plug and play, eliminating downtime and optimising spares holding.
A typical solution is a system comprising multiple radio RTUs (outstations), interfaced into a SCADA system using an onboard ethernet port. This simple plug-and-play system has one RTU housed at the local control end, with all the inputs and outputs dedicated to control and feedback status via the ethernet connection, and another located remotely hardwired to the pump electrical control and any instrumentation. The only necessary wiring is for the power supply and any required control circuits.
Unlike traditional systems, simple configuration templates on each unit are edited to share the I/O status between each RTU. For example, if a switch on one side is triggered, it will promote an output on the other side to turn the pump on or off. This makes programming a line of code unnecessary. A simple wireless solution that needs no programming will reduce expenditure by saving time and resources.
The system ensures mines can monitor the conditions of their pumps wirelessly over distances of up to 20km. The RTUs are also robust, housed in a weatherproof casing with power supply charger units and backup batteries. What’s more, the low power consumption of the system makes it suitable for solar power outstations at remote reservoirs.
Easy-to-use
With any remote monitoring system, ease of use is imperative to ensure efficient and productive operations. Therefore, a wireless distributed RTU with data acquisition capability is a no-brainer over cable-based systems. The units can be interfaced with an existing SCADA or DCS system via onboard Ethernet ports. This makes installation quick and simple, and plant managers also save on additional hardware and engineering time.
Once collected, all data can be viewed on fully customisable HMIs. Operators can easily review their pump and view statuses and alarm conditions on an LED touch screen from any connected HMI. Adding Omniflex’s cloud-based Data2Desktop service also allows plant managers to reap the benefits of remotely monitoring their site using a tablet or phone, rather than having to be onsite at a PC.
Mining is a productivity-driven operation, and downtime is lost revenue that can’t be recovered. When plant assets are spread over a large area, wireless remote monitoring technology makes control and management more simple, efficient and cost-effective.