Stirring things up: Submersible mixers support huge wastewater treatment project
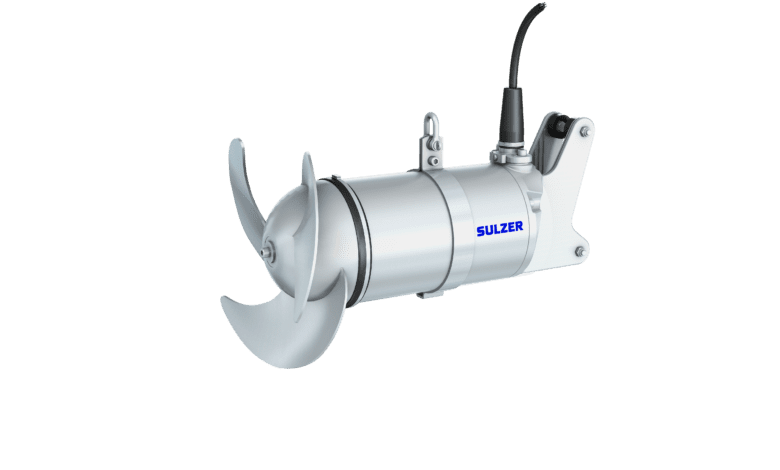
As part of one of the largest investments in Europe for wastewater treatment, a plant near Naples, Italy, was equipped with innovative technologies to improve water quality while minimising energy usage. At the core of effective denitrification operations are Sulzer’s XRW 400 submersible mixers with a permanent magnet motor, which could cut energy costs by up to EUR 45,000.
The large-scale project aims to improve the quality of the coastal environment and the waters around Naples by revamping and upgrading key water and wastewater treatment facilities in the region. This program represents the most considerable European investment in water purification and decontamination for the past 20 years, supporting the treatment of wastewater from over 4.5 million inhabitant equivalents (900’000m3 of water per day) in the region.
One of the five facilities selected is among the largest in Europe. Established in the 1970s, it gathers wastewater from a large area in the northern part of Naples and has a processing capacity of 240’000m3 of water per day (1.2 million inhabitant equivalents). To continue supporting the region, key improvements were required to optimise the sewage treatment process and energy consumption while ensuring regulatory compliance.
An innovation tank
To meet the objectives set out for the successful re-functionalisation and modernisation of this infrastructure, a leading water and waste service specialist contacted Sulzer. The companies have a longstanding relationship, and through multiple international collaborations, the specialist has been able to learn more about Sulzer’s state-of-the-art technologies and services, growing its confidence in the ability of its partner to deliver well-suited solutions. In particular, there was enthusiasm to adopt 28 of Sulzer’s highly energy-efficient mixers, such as the XRW 300 range of submersible units, for the 14 denitrification tanks within the wastewater treatment plant.
Used to remove nitrogen from wastewater effluents, the tanks installed in the facility have an unusual geometry, being 22m long but only 7.85m wide and 4.8m high. Therefore, it was necessary to specify mixers featuring propellers with a limited diameter, which are typically regarded as difficult to adjust in order to minimise energy usage.
Elisabetta Sardi, Area Manager at Sulzer, explained: “To address the specific needs of this application, we suggested the use of our XRW 400 submersible mixers. These are extremely compact, delivering effective processing of wastewater, and are equipped with Premium Efficiency IE3-equivalent, sensorless, permanent magnet motors that are controlled by variable frequency drives.
“This means that they can adjust their speed to suit the real-time environmental conditions rather than maintaining a set speed at all times. As a result, it is possible to reduce energy use whenever possible, delivering significant benefits when it comes to operational costs and environmental performance.”
Driving performance
In practice, the use of conventional solutions with IE3-equivalent, three-phase, squirrel-cage motors could reduce energy costs by €8,000 at the plant.
Conversely, the XRW 400 series could slash such expenditures by more than five times, delivering savings of up to €45,000. Even more, the presence of drives supports self-cleaning functions, enhancing the service life of the mixers in such challenging applications while reducing downtime, maintenance activities and their associated costs.
Following the installation, commissioning and startup of Sulzer’s submersible mixers, the plant and its denitrification tanks have been running smoothly. These have efficiently processed large volumes of wastewater daily while meeting environmental standards for effluents.
Elisabetta commented: “We are very happy with our collaboration on this project. The XRW 400 mixers are the first to run via permanent-magnet motors and represent the only solution of this kind that would meet the equipment specifications for the denitrification tanks. We are sure there will be many other treatment plants that will look to collaborate with us and achieve similar benefits.”